PDCAサイクルの基本とは?
PDCAサイクル(Plan-Do-Check-Act)は、ビジネスのプロセスや製品の継続的な改善を目指す管理手法です。デミングサイクルやシューアートサイクルとも呼ばれるこの方法論は、1920年代にウォルター・シューハートによって初めて提唱され、その後、エドワーズ・デミングがさらなる改良を加えました。現代のビジネス環境においても、このサイクルは多くの企業で活用されており、その基本的な概念を理解することは非常に重要です。
PDCAサイクルの歴史と意義
デミングサイクルの起源
PDCAサイクルは、1920年代にウォルター・シューハートがベイ・ベル電話研究所で開発した「Plan-Do-See」モデルに由来します。シューハートの弟子であるエドワーズ・デミングがこのモデルを改良し、1940年代に「Plan-Do-Check-Act」サイクルとして広く知られるようになりました。デミングは、日本の製造業にこのサイクルを導入し、それが品質管理の基盤となりました。
現代への適応
現代のビジネス環境では、PDCAサイクルは多様な分野で応用されています。特に、技術革新が急速に進む中で、PDCAの各ステップを適切に実行することで、改善のスピードと質が向上します。多くの企業がPDCAサイクルを基にした管理手法を取り入れており、その成果は顕著です。
PDCAサイクルの4ステップ詳細解説
計画段階
計画段階は、問題を特定し、その解決策を計画するプロセスです。この段階では、目標を設定し、達成するためのプロセスやリソースを具体的に策定します。現状のデータ分析や市場調査を行い、最適な戦略を立案します。
実行段階
実行段階では、計画段階で立てた計画を実際に実行します。このステップでは、具体的な行動計画に基づき、目標達成に向けたアクションを実行します。実行過程でのデータ収集や進捗状況のモニタリングも重要です。
検証段階
検証段階では、実行されたアクションの結果を評価します。得られたデータを元に、計画通りに進んだかどうかを確認し、必要に応じて改善点を洗い出します。この段階でのフィードバックは、次のPDCAサイクルにおける計画段階で非常に重要な役割を果たします。
行動段階
行動段階は検証結果を元に改善策を実行するプロセスです。ここでの主な目標は、特定された問題点を解決し、プロセス全体の質を向上させることです。この段階での反省と改善は、次のサイクルの計画段階において更なる高品質な計画策定の基盤となります。
PDCAサイクルの限界と課題
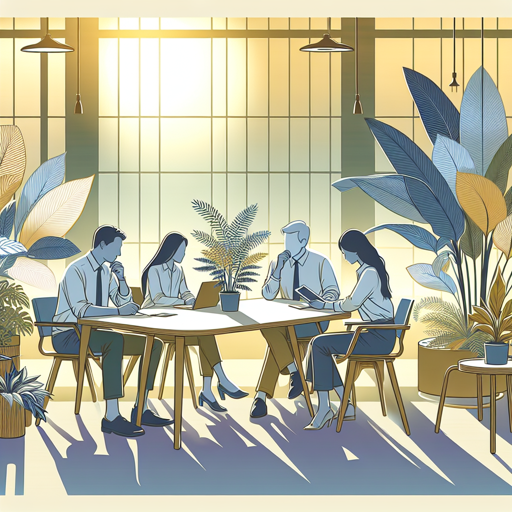
PDCAサイクル(Plan-Do-Check-Act)は多くの企業で活用されている管理手法ですが、現代のビジネス環境においてはその限界と課題が浮き彫りになってきています。本記事では、PDCAサイクルの限界と共に、それに対する課題について詳しく解説します。
理論と実践のギャップ
PDCAサイクルは理論的には非常に効果的な手法ですが、実際の現場で実践する際には多くのギャップが存在します。
現場のバリエーション
現場の状況は企業ごとに異なり、どの部門でも一律にPDCAサイクルを適用することは難しい場合があります。例えば、製造業とサービス業では業務プロセスが大きく異なり、PDCAサイクルのステップがうまく適合しないことがあります。現場のバリエーションを考慮せずに一括して導入すると、かえって混乱を招くことがあります。
データ分析の重要性
PDCAサイクルの中で「検証(Check)」のステップは、データ分析と結果の評価を必要とします。しかし、多くの企業では適切なデータ収集と分析が行われておらず、その結果、正確な評価や改善策の導出が困難となっています。データ分析のスキルが不足している場合、PDCAサイクルの効果は半減してしまいます。
組織文化との相性
PDCAサイクルがうまく機能するかどうかは、企業の組織文化との相性にも大きく依存します。
社員のモチベーション
PDCAサイクルの成功には、社員一人ひとりが積極的に関与し、改善活動に取り組む姿勢が求められます。しかし、モチベーションが低い組織では、PDCAサイクルを導入すること自体が困難です。特に、トップダウンの文化が強い組織では、現場の意見が反映されにくく、改善活動が形骸化しがちです。
コミュニケーションの課題
PDCAサイクルの各ステップは、部門間および社員間の綿密なコミュニケーションを必要とします。コミュニケーションが不足している企業では、情報共有やフィードバックが遅れ、サイクルの進行が停滞することがあります。特に大規模な組織では情報の伝達が難しく、PDCAサイクルが滞る原因となることが多いです。
現代のビジネス環境においてPDCAサイクルを効果的に機能させるためには、これらの限界と課題に対処し、企業ごとにカスタマイズされたアプローチが必要です。次回は、新しいアプローチについてもご紹介します。
現代ビジネスにおける新しいアプローチ
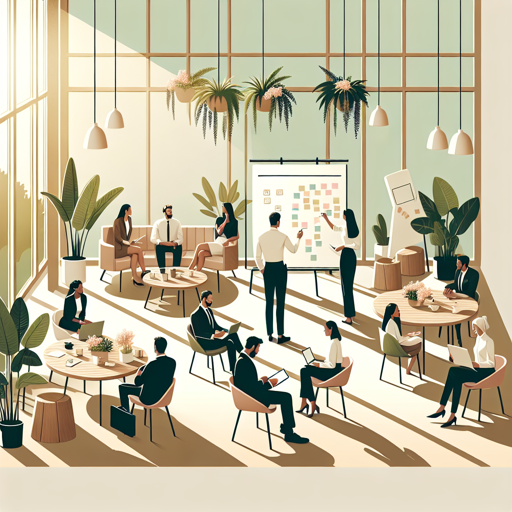
現代のビジネス環境は急速に変化しており、従来のPDCAサイクルだけでは対応が難しい場合があります。そこで、アジャイル手法やリーン生産方式などの新しいアプローチが注目されています。これらの手法は、変化に対応しやすい柔軟なプロセスを提供し、持続的な改善を促進します。
アジャイル手法とスクラム
アジャイル手法とスクラムは、ソフトウェア開発の分野で特に人気があり、多様なプロジェクト管理に応用されています。
アジャイルの基本概念
アジャイルは、迅速な対応と顧客満足を重視したプロジェクト管理手法です。計画を立て、短期間で実行し、その結果を基に改善を図ることを繰り返すことで、柔軟に変化に対応することを目的としています。アジャイルの基本概念には、反復的かつ漸進的な開発、自己組織化チーム、顧客との協力が含まれます。これにより、開発プロセスがより透明で反応的になるのです。
スクラムの実践
スクラムは、アジャイル手法の一種であり、具体的な実践方法を提供します。スクラムは、固定された短期間のスプリントを通じてプロジェクトを進行し、スプリントごとに成果物を提供します。スクラムチームは、スクラムマスター、プロダクトオーナー、そして開発チームから構成されます。スクラムの実践には、デイリースクラムミーティングやスプリントレビュー、レトロスペクティブなどのイベントが含まれます。これにより、チームは継続的に改善と適応を行うことができます。
リーン生産方式
リーン生産方式は、トヨタ生産方式(Toyota Production System, TPS)から発展した手法で、不要な浪費を排除し、価値を最大化することを目指します。
リーンの原則
リーンの基本原則には、価値の定義、価値の流れの識別、フローの確立、プル方式の導入、そして無駄の持続的な排除が含まれます。これらの原則は、製品の品質向上や生産効率の最適化に寄与します。また、リーンは従業員の創造力と知識を最大限に活用することを強調し、持続的な改善文化を育むことを目指します。
具体的な事例
リーン生産方式の具体的な事例として、トヨタ自動車が挙げられます。トヨタは、ジュストインタイム(Just-In-Time, JIT)と呼ばれる在庫管理手法や、カンバン方式を導入し、生産の効率性と適応力を向上させています。また、他の多くの企業もリーン生産方式を取り入れ、無駄の排除とプロセスの最適化を図っています。これにより、品質向上とコスト削減を実現し、顧客満足度の向上にも寄与しています。
現代ビジネスにおいて、これらの新しいアプローチを導入することにより、企業はより柔軟かつ効率的に目標を達成することができます。次回は、これらの手法がどのように企業の成功に寄与するかについて詳しく解説します。
PDCAサイクルと新しいアプローチの統合
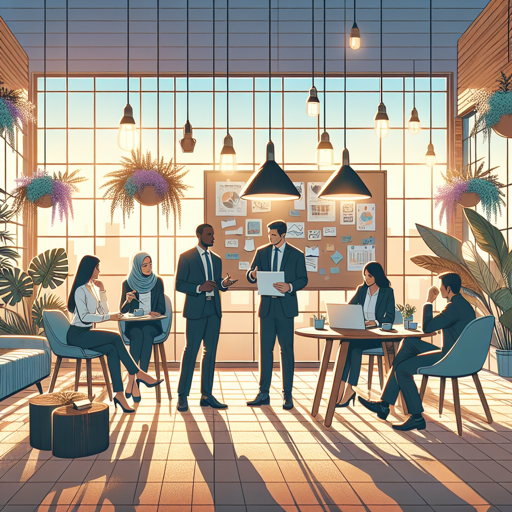
現代のビジネス環境では、単一の管理手法では限界が生じることが多いため、PDCAサイクルと他の新しいアプローチの統合が求められています。PDCAサイクルの強みを活かしつつ、アジャイル手法やリーン生産方式などの新しいアプローチを取り入れることで、より柔軟で効果的な管理が可能になります。
ハイブリッド型のアプローチ
ハイブリッド型のアプローチは、PDCAサイクルと新しい手法を組み合わせることで、双方の利点を活かし効率的に改善を進める方法です。
PDCAとアジャイルの融合
PDCAサイクルとアジャイル手法の融合は、特にソフトウェア開発などの迅速な変化が求められる分野で効果を発揮します。PDCAの計画(Plan)、実行(Do)、検証(Check)、行動(Act)のサイクルを維持しつつ、アジャイルのスプリントやデイリースクラムを取り入れることで、短期間での改善と適応が可能となります。この融合により、プロジェクトの柔軟性が高まり、迅速なフィードバックと適応が実現します 。
リーンとPDCAの統合
リーン生産方式とPDCAサイクルの統合もまた、多くの企業で実践されています。リーンの価値の流れの識別、フローの確立、プル方式の導入などの原則をPDCAサイクルと組み合わせることで、無駄の排除と持続的な改善が実現します。例えば、トヨタはPDCAサイクルを基盤としながらも、カンバン方式を利用して生産プロセスを最適化しており、その結果、高い品質管理と効率性を維持しています 。
事例紹介
具体的な事例を通じて、PDCAサイクルと新しいアプローチの統合がどのように成功を収めているか、あるいは課題に直面しているかを紹介します。
成功事例と失敗事例
成功事例としては、ソフトウェア開発企業がアジャイル手法とPDCAサイクルを融合させたことで、迅速なリリースサイクルを実現し、顧客満足度を高めたケースがあります。一方で、失敗事例としては、組織間でのコミュニケーション不足が原因でPDCAサイクルがうまく機能せず、改善活動が停滞したケースもあります。このような事例を分析することで、統合アプローチのメリットとデメリットを明確にすることができます 。
統合アプローチのメリット
統合アプローチの主なメリットは、柔軟性と適応力の向上です。PDCAサイクルと他の手法を組み合わせることで、変化する環境に迅速に対応できるようになり、持続的な改善が促進されます。また、リーン生産方式と統合することで、無駄が削減され、生産効率が向上します。さらに、アジャイル手法との融合により、チーム全体での協力とコミュニケーションが強化され、より統一された目標に向かって取り組むことができます 。
現代ビジネスにおいて、これらのハイブリッド型のアプローチを導入することで、企業はより効果的かつ効率的に目標を達成することが可能となります。次回は、具体的な戦略と方法についてさらに詳しく解説します。
未来に向けた展望
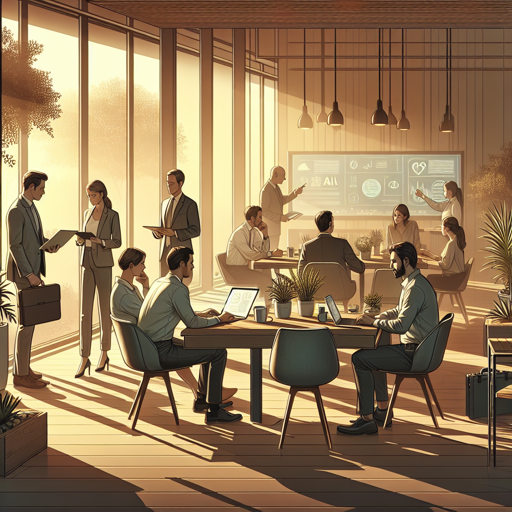
ビジネス環境は急速に変化し続けており、PDCAサイクルや他の従来の管理手法だけでは完全に対応しきれない場合があります。そこで、組織は新しいアプローチを取り入れることで、さらなる成長と競争力の維持を目指す必要があります。ここでは、継続的な改善の重要性と新技術の連携について考察します。
継続的改善の重要性
継続的改善(Continuous Improvement, CI)は、組織が持続的に成長し、競争力を維持するために不可欠な要素です。改善活動を日常業務に組み込み、社員が持続的に改善を追求する文化を築くことが重要です。
学びと成長の文化
学びと成長の文化は、企業が持続的に進化し続けるための基盤です。この文化では、全ての社員が積極的に問題を見つけ、改善策を提案し、実行に移します。失敗を恐れず、各自が学びながら成長する環境を提供することで、企業全体のパフォーマンスが向上します。
企業全体への浸透
継続的改善の文化を企業全体に浸透させるためには、トップダウンとボトムアップのアプローチの両方が重要です。経営陣が継続的改善の価値を強調し、その重要性を全社に伝える一方で、現場の社員が自発的に改善活動に参加することが求められます。このように、全てのレベルで持続的改善が行われることで、組織全体の効率と生産性が向上します。
新技術との連携
現代のビジネスでは、新技術を活用することで、継続的改善のプロセスをさらに強化することが可能です。特にAIやIoTといった先端技術の活用が注目されています。
AIとデータ分析の活用
AI(人工知能)とデータ分析は、継続的改善のプロセスにおいて非常に重要な役割を果たします。AIは大量のデータを迅速に分析し、パターンや異常を検出することができるため、改善のためのインサイトを提供します。これにより、より正確な意思決定と迅速な対応が可能となり、ビジネスの競争力が向上します。
IoTとリアルタイムデータ
IoT(インターネットオブシングス)は、様々なデバイスやシステムからリアルタイムでデータを収集・分析する技術です。これにより、現場の状況をリアルタイムで把握し、迅速かつ効率的な対応が可能になります。例えば、製造現場では、センサーを用いて設備の状態をモニタリングすることで、故障の予兆を早期に検知し、未然に防ぐことができます。これにより、ダウンタイムの削減と生産性の向上が実現します。
未来に向けた展望として、これらの新しいアプローチを取り入れることで、組織は変化に柔軟に対応し、持続的に成長することが可能となります。次回は、これらの技術が具体的にどのようにビジネスに応用されているかについて詳しく解説します。